Grasping About Aluminum Casting: Methods Demystified
Grasping About Aluminum Casting: Methods Demystified
Blog Article
Opening the Potential of Light Weight Aluminum Casting: Proven Strategies for Success
Light weight aluminum casting has actually long been acknowledged for its flexibility and prevalent applications across various markets - about aluminum casting. However, revealing the full possibility of this process calls for more than simply basic expertise. By applying tested approaches developed via years of industry experience and technology, producers can boost their light weight aluminum casting procedures to new elevations of efficiency and high quality. From maximizing design factors to consider to improving manufacturing processes, the essential hinge on harnessing these methods properly. Join us as we explore the essential aspects that can propel aluminum casting in the direction of unparalleled success in today's competitive market landscape.
Advantages of Aluminum Casting
One of the main advantages of aluminum spreading is its lightweight nature, which contributes to fuel efficiency in markets such as automobile and aerospace. Additionally, aluminum is very flexible, enabling for complicated and elaborate shapes to be conveniently created through spreading procedures.
Additionally, aluminum spreading supplies outstanding deterioration resistance, making it ideal for applications where direct exposure to severe environments is a problem. The material also displays good thermal conductivity, which is beneficial for markets needing heat dissipation, such as electronic devices (about aluminum casting). Light weight aluminum is fully recyclable, lining up with the expanding emphasis on lasting practices in modern-day manufacturing.
Style Factors To Consider for Casting
When thinking about casting design, careful focus to detail is paramount to make sure the effective production of high-grade components. The style stage plays a vital role in the general success of a light weight aluminum casting job. One vital consideration is the choice of ideal geometries and features that assist in the spreading process. Developers have to take into consideration elements such as draft angles, fillets, and wall surface density to guarantee appropriate steel circulation and solidification during casting.
Moreover, factors to consider associated with parting lines, gating systems, and risers are necessary to avoid flaws like porosity and contraction. It is crucial to optimize the design for efficient material use and minimize post-processing requirements. Simulations and prototyping can be beneficial tools in evaluating and fine-tuning the spreading layout prior to major manufacturing.
Cooperation in between style suppliers, designers, and factories is essential to attend to any type of prospective challenges early in the design stage. By integrating these considerations into the casting style process, suppliers can boost product quality, decrease costs, and inevitably unlock the full possibility of aluminum spreading.
Enhancing Casting Effectiveness
When intending to boost casting efficiency in light weight aluminum spreading jobs,Creating with a focus on enhancing product flow and lessening issues is important. To accomplish this, making use of simulation software can aid in identifying prospective concerns before the casting process begins. By simulating the flow of molten light weight aluminum, developers can adjust gating and riser styles to make sure appropriate dental filling and solidification, ultimately decreasing the incident of defects such as porosity or shrinkage.
Furthermore, implementing appropriate warmth therapy processes can enhance the overall casting effectiveness. Warm therapy can aid improve the mechanical buildings of the light weight aluminum spreading, ensuring that the final component meets the required specs. Furthermore, utilizing automation and robotics in the casting process can improve production, decrease hands-on labor, and boost general effectiveness.
Moreover, constant tracking and quality assurance during the casting procedure are critical for identifying any deviations and ensuring that the last items satisfy the desired standards. By implementing these strategies, manufacturers can boost casting performance, enhance product quality, and inevitably accomplish higher success in aluminum spreading jobs.
Quality Assurance in Aluminum Spreading
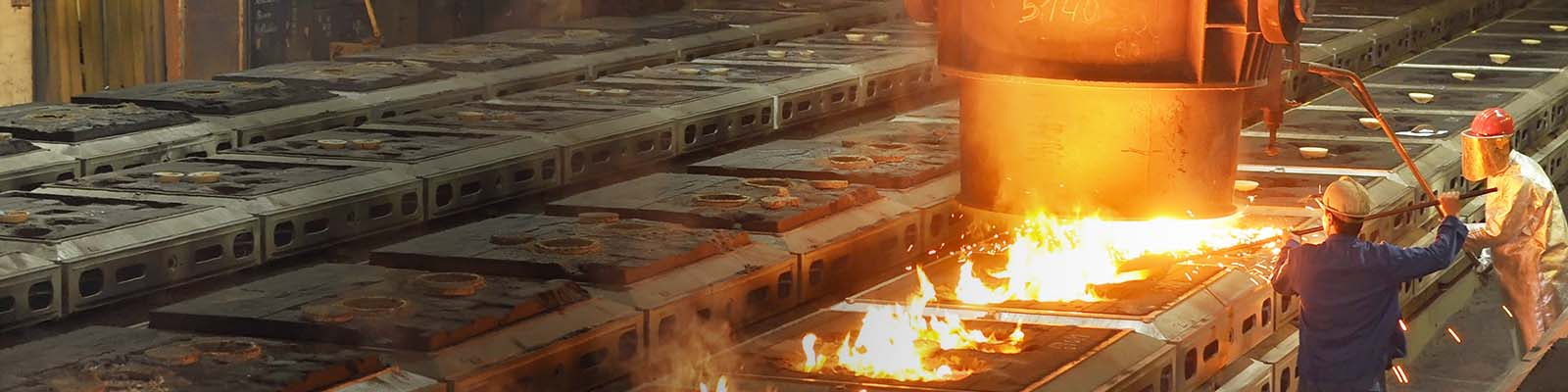
Reliable quality assurance techniques play a pivotal function in making sure the accuracy and integrity of aluminum casting processes. Quality assurance actions in aluminum casting encompass a variety of tasks targeted at promoting specific standards and determining discrepancies that might jeopardize the end product. These techniques start with the mindful option and inspection of raw materials to assure their quality and viability for the casting procedure. Monitoring and managing the specifications of the casting process itself, such as pressure, temperature level, and air conditioning prices, are crucial action in keeping uniformity and stability in the final products.
In enhancement to process control, top quality control in light weight aluminum casting includes strenuous screening and inspection treatments at different phases of manufacturing. By implementing robust high quality control methods, light weight aluminum spreading facilities can provide items see here now that fulfill consumer expectations for high quality, efficiency, and integrity.
Optimizing Productivity
To achieve optimum monetary performance, an extensive strategy for making best use of earnings within aluminum spreading operations must be diligently developed and executed. One vital element of making the most of productivity in aluminum spreading is enhancing manufacturing efficiency.

In addition, expanding item offerings and checking out new markets can help increase earnings streams. Recognizing client requirements and market trends can guide critical choices to utilize on emerging opportunities. Investing in r & d to introduce processes or items can likewise drive success with distinction and client complete satisfaction.
Conclusion
Finally, light weight aluminum casting supplies various advantages in terms of design versatility, resilience, and cost-effectiveness. By meticulously considering layout considerations, improving casting efficiency, executing high quality control steps, and maximizing earnings, manufacturers can unlock the complete potential of aluminum spreading. This trustworthy and versatile process has confirmed to be a discover this info here successful option for a variety of commercial applications.
Additionally, aluminum is extremely flexible, permitting for intricate and detailed shapes to be easily created via spreading processes.Efficient quality control methods play an essential duty in ensuring the precision and dependability of light weight aluminum spreading procedures.In enhancement to process control, high quality control in light weight aluminum spreading includes extensive screening and examination procedures at different phases of manufacturing. By executing durable high quality control methods, light weight aluminum spreading facilities can provide products that satisfy client expectations for efficiency, integrity, and high quality.
By very carefully thinking about style considerations, enhancing casting performance, applying quality control procedures, and maximizing productivity, suppliers can unlock the full possibility of light weight aluminum casting.
Report this page